Safety Checklist Program for Schools
October 2003
DHHS (NIOSH) Publication Number 2004-101
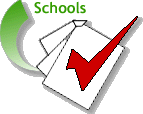
Chapter 2: How to Establish an Effective Occupational Safety and Health and Environmental Safety Program
Overview
The key to preventing harm to school employees, students, and the environment is to establish a good occupational safety and health and environmental safety program.
A good program may take years to put in place, but the guidelines below are a good place to begin. Use the items next to the boxes to create a checklist of your progress. Start with individual items or parts of items. The guidelines are divided into five sections:
- Assure management commitment
- Assure employee and student involvement
- Identify and prioritize potential hazards
- Eliminate hazards
- Train employees, students, and management
The occupational safety and health and environmental safety program should be tailored to the needs of your school or organization. The program may be district-wide or developed solely for career-technical and career orientation classes, depending on school resources. Small school districts with limited resources have formed safety and health cooperatives with other districts to help manage all or parts of their programs.
Assure Management Commitment
- Top administration must be involved
The school board, superintendent, school principal, and top school administrators should all be leaders in implementing the program. They should stay informed and involved. - Develop a written safety and health policy
Top administration should issue a written policy supporting a safe and healthy environment in the schools. This policy may take the form of one or more policy statements or a policy manual that covers issues ranging from safety procedures to energy conservation. It should be posted and/or issued to all employees and students. - Assure adequate personnel resources
Assign appropriate individuals responsibility for the functions listed in the remaining sections of this chapter. Make sure they are given adequate time to do the job. It is important to select people who are competent and motivated, and who have the skills and adequate resources to do the job. - Assure adequate financial resources
Money must be allocated for the safety and health program. Make sure the appropriate parties (school board, administration, teachers) plan for environmental and safety needs during the budget process, so that there are funds to support these programs. - Evaluate Program performance regularly
The occupational safety and health and environmental safety program should be a part of all performance reviews, including those of top administration, teachers, and students. Acknowledge those who have been involved in identifying and correcting hazards and working safely.
Assure Employee and Student Involvement
- Establish a Hazard Prevention Committee
A Hazard Prevention Committee should be composed of representatives of management, school employees, and perhaps students. For such a committee to succeed, it should be selected carefully; have a clear idea of its mission, power, and functions; and be skilled in conducting effective meetings.This committee can do the following:- Take on many of the functions described below that are too much for any one person
- Seek immediate input from all areas of the school, such as the classroom, maintenance, and purchasing
- Brainstorm by creatively combining and modifying ideas from many perspectives
- Improve communication among the various representatives
- Prioritize hazard controls, training, and other activities in a way that is satisfactory to all parties
- Establish a procedure for reporting potential hazards using a written form.
- Communicate regularly
Use newsletters, bulletin boards, pay check envelopes, and class time to communicate new procedures and new safety assignments and to introduce new committee members. Keep the program on people's minds. Make safety, health, and the environment a regular item on the agenda of staff, board, union, and PTA meetings. Post committee minutes, reports, surveys, and (especially) memos referring to problems, solutions, and achievements. - Develop a hazard-reporting procedure
Students and employees should be encouraged to look for and report potential hazards to the Safety and Health Coordinator, or to the chairperson of the Hazard Prevention Committee. Students may also report hazards to a teacher, the School Principal, or to another responsible adult. The person who discovers the hazard should then fill out the designated form and submit it to the Safety and Health Coordinator for follow-up action. Students should fill out this form with the help of the Safety and Health Coordinator.
Identify and Prioritize Potential Hazards
The following functions should be performed on a regular basis by individuals or committee members assigned to the task. You may wish to keep computerized records of these activities.
- Complete the checklists in the Safety Checklist Program manual
Chapter 3: Implementing a Safety Checklist Program will help you in using the checklists. The checklists can help you to identify hazards and determine whether or not your organization is in compliance with applicable safety and health regulations. - Conduct walkthrough inspections
Using the checklists also provides an opportunity to interview employees and students about their concerns. Let them know the outcome of previous concerns and hand out new hazard report forms. For ideas about ways to use the checklists in this manual to teach students, see Appendix B: Using the Safety Checklists to Teach Students About Occupational Safety and Health. - Maintain and update a chemical inventory
As required by the OSHA hazard communication program, the Superfund Amendments and Reauthorization Act (SARA) Title III, and State hazardous waste regulations, you must record the names and amounts of all chemicals used, the means of disposal used, and the occurrence of any spills or releases on the premises. - Maintain and update a process and equipment inventory
Record the location of hazardous processes or equipment, and the dates when maintenance or monitoring must be performed. Also keep an inventory of the safety equipment and those who use it. - Establish a procedure for purchasing goods and services and leasing new space
Avoiding a hazard is easier than controlling it. Before any purchase of chemicals, equipment, or services, develop a system that may be reviewed by a safety representative or committee member. Similarly, review plans for renovating, constructing, or leasing new facilities. - Investigate incidents, spills, and releases
Chemical release and other incident report forms should have a space to answer, "What were the causes of the incident or release?", and "What precautions or controls could have prevented the incident or release?" A safety representative or committee member should investigate every incident or release to determine how to prevent such a problem in the future. Employees and students should be encouraged to report "near hits" or "close calls" as well. - Review injury and illness records
Review reports of injuries, the OSHA Log 300 data (a required employee occupational illness and injury record-keeping system), personal injury claims, and workers' compensation claims to identify whether certain classrooms, buildings, or processes pose an excess risk. - Review environmental records
Look at the hazard communication inventory, air permits, hazardous waste records, solid waste records, and medical waste records to identify chemicals or processes that should be substituted, recycled, or prevented. - Order and review environmental, personal, and biological monitoring data
A few processes in career-technical education programs may require air monitoring, environmental sampling, or biological monitoring of employees' blood or urine. Consider consulting outside experts to determine which procedures to use. The Appendix A: Resource Agencies and Organizations can help identify ways to locate the appropriate consultant. - Arrange for medical screening
A few processes in career-technical education programs may require medical screening. In particular, all employees and students who wear respirators should be evaluated by a physician to determine whether they are fit to wear one. Crucial to respirator wearing is proper fit-testing and training provided by the school. Those exposed to excess noise need periodic hearing tests, the results of which should be tracked over time. Personal protective equipment (PPE) (e.g., respirators, hearing protection) should be provided by the school. Video display operators should get regular eye exams. As with the guideline above, consider consulting outside experts to determine which screening tests to use. Refer to Appendix A: Resource Agencies and Organizations for ideas about locating consultants.
Eliminate Hazards
The following functions should be performed by individuals or committee members assigned to the task.
- Develop written procedures and programs
Certain processes require written safety procedures in addition to the written safety and health program plan. Examples include emergency planning, respiratory protection, vehicle safety, and hazard reporting. - Develop emergency response plans and procedures
For assistance in preparing plans to deal with chemical spills, see Appendix D: Emergency Procedures in Schools in the Event of a Chemical Spill. - Provide regular equipment maintenance, repair, and replacement
Equipment includes hazardous machinery, safety gear, and the ventilation system. Check that machine guards are in place. Implement a maintenance and repair record-keeping system as well. - Perform routine housekeeping
Get rid of rubbish by disposing of it properly. Check to make sure that rubbish, hazardous chemicals, and other trash are properly stored and that exits are not blocked. - Install engineering controls
The best way to make a process safe for people and the environment is by designing it to be safe. Incorporating safety and health controls in the design of the process is more reliable than having students follow certain rules, wear protective gear, or clean up excess pollution. The safety and health controls that are built into a process are referred to as “engineering controls.” Engineering controls are the first in the hierarchy of controls that are used to reduce teachers' and students’ exposure to a hazard. The order in which these controls are considered is as follows: (1) engineering controls, (2) administrative controls, and (3) personal protective equipment (PPE). Engineering controls may include substitution, isolation, enclosure, and ventilation of a process or equipment. Administrative controls include training in hazard recognition and schedule changes or reduced work times to decrease students' exposures. PPE may include respirators, aprons, safety goggles, hard hats, hearing protection, and welding masks. Committees are a useful means for brainstorming ideas about engineering controls or substitute processes. Advice from outside experts may also be helpful (see Appendix A: Resource Agencies and Organizations ). - Provide personal protective equipment (PPE)
Use of respiratory protection should be a temporary or last-resort solution when engineering controls are inadequate to control the hazards. However, respirators could be used routinely if job hazards require it. Other forms of PPE such as hearing protection, welders' masks, hard hats, and safety goggles could be required depending on the job and hazards involved. Using protective gear involves careful selection, maintenance, and user training. - Install eye wash facilities and showers
Install eye washes and/or showers near battery-changing stations, maintenance operations, heating and ventilating operations, and other processes that use corrosive chemicals or emit irritant aerosols. - Work cooperatively with inspectors from regulating agencies
Remember that the purpose of regulations is to ensure that employers maintain a safe and healthy work environment. Inspectors can often identify ways to control hazards found during an inspection (see Appendix C: Suggestions for Facilitating Inspections). - Seek expert advice
Difficult problems are often handled best by using a committee of all involved parties to brainstorm solutions. However, you may need outside advice. Your State Department of Education, county superintendent's office, EPA, OSHA, the local fire department, or your local branch of the American Industrial Hygiene Association (AIHA) or National Safety Council (NSC) are sources of free advice or referral to an appropriate consultant or organization. See Appendix A: Resource Agencies and Organizations for addresses and phone numbers of some of these organizations.
Train Employees, Management, and Students
- Train all new employees and students
The safety training should be conducted before employees or students start a career-technical program or course. This training can be built into basic orientation and the curriculum. - Provide mandated training programs to employees and students
Depending on the types of classes your school provides, training may be required on emergency and fire prevention, fire extinguishers, respiratory protection, occupational noise exposure, woodworking machinery, welding, asbestos handling, hazard communication, and hazardous waste handling. Training is also recommended for video display terminal operators. Direct supervisors should receive the same training as their students or subordinates. - Train safety representatives and hazard prevention committees
Training can enhance the ability of students and employees to carry out the functions listed above. In particular, they may wish to obtain training in computerizing the program, investigation of injuries or other incidents, safety and environmental record-keeping, hazard identification and control, industrial hygiene fundamentals, or environmental regulations. Outside training opportunities provide an essential means for safety, health, and environmental personnel to network with and learn from programs in other schools. - Obtain training help from the regulating agencies
Often training help can be provided by regulating agencies or local industry.
Teachers, safety committees, and supervisors should not be discouraged if only small parts of an occupational safety and health and environmental safety program are in place early in the program. It takes time, money, and persistence to have a good program. Each new step is a great improvement over the way things were run before the program was in place.
- Page last reviewed: June 6, 2014
- Page last updated: June 6, 2014
- Content source:
- National Institute for Occupational Safety and Health Education and Information Division