Cargo Handler Killed By Airplane Tail Stand Tip-Over During Transport
New Jersey Case Report: 07NJ038
Report Date: December 11, 2008
Summary
A tip-over of an airplane tail stand while it was being moved resulted in the death of a male cargo handler at a major New Jersey airport. The tail stand tip-over occurred when the cargo handler was using a cargo tug vehicle to return the tail stand to its storage location after the offloading and loading of cargo on a Boeing 747 aircraft. During transit, the support pad of the tail stand's central stabilizer, which was left in the down position, caught the lip of a manhole cover that extended 5/8" above the paved surface. This snag of the central stabilizer support pad on the edge of the manhole cover caused the tail stand to flip forward and strike the cargo handler in the head, neck, and back before pinning him to the steering wheel of the tug. The tail stand, which weighs approximately 1,750 pounds, caused massive traumatic injuries to the cargo handler who was pronounced dead at the hospital one hour later. Approximately one hour before the fatal incident, a different tail stand in use on site was damaged when the central stabilizer was similarly left in the down position, causing it to catch on the edge of the same manhole cover; however, corrective action was not taken. NJ FACE investigators recommend following these safety guidelines to prevent similar incidents:
- Airport vehicular tugs should be equipped with overhead protective cages to prevent injuries caused by strikes from objects falling from above.
- Employees assigned to move and handle tail stands, as well as other large equipment, should receive detailed training on the safe work practices and potential hazards associated with this task.
- Proper use and safe handling signage should be clearly visible on all equipment, including tail stands. This signage is critical for reminding workers about proper and safe handling practices, such as raising the central stabilizer of the tail stand before attempting to move it. The warning labels should be prominent and clearly convey the seriousness of the hazard.
- Employees must be given the appropriate amount of time to perform tasks required for successful completion of their job duties.
- Maintenance records for heavy equipment must be reviewed frequently. If repeat incidents or problems are noted, corrective action must be taken in order to correct equipment damage that could lead to injuries of employees.
- Safety devices for aircraft tail stands that prevent moving the stand without the outriggers and central stabilizer in the correct position should be designed and integrated into the construction of the tail stand.
- Employees should discuss, and management should actively seek, information related to potential problems or near-misses encountered by employees while performing work tasks. All near-misses should be carefully evaluated and preventive actions should be taken.
Introduction
The incident site was a large airport that included cargo and baggage handling as well as passenger service. The company that was involved in this incident handled passenger bags, luggage, and freight that was transported via aircraft. Many planes not only have passenger luggage compartments, but also may contain a central cargo bay in the center of the aircraft that can receive 12-foot-high pallets of cargo. The business is extremely time sensitive and requires the movement of cargo quickly to keep the planes on schedule.
Back to Top
Investigation
The incident occurred at a major international airport in New Jersey on May 29th, 2007, at 12:32 am during the completion of cargo handling routines for a Boeing 747 aircraft. This plane carried both passengers and cargo. The location of the incident was in an area often referred to by employees as "the ramp," which is essentially the exterior area of the airport adjacent to the terminal gates and maintenance hangers. The cargo handling crew normally consists of four members, but on the date of the accident the crew consisted of only three members. The crew was rushed because the flight was late and there was an urgency to accomplish the offloading of incoming cargo and loading of outgoing cargo onto the plane to meet strict schedules. In addition, the decedent was working his second consecutive eight-hour shift. The facility operates three shifts per day, seven days per week. Visibility and lighting were adequate on the ramp and the weather was clear and dry.
The tail stand (see Figure 1) weighed approximately 1,750 pounds and was towed to and from aircraft by a cargo tug, which is a common small vehicle used at many airports. Tail stands are necessary because 747 aircraft specifically require support of the airplane tail during loading and offloading of cargo. The cargo tug involved in this incident did not have an overhead protective cage. However, there was another cargo handling company at this airport that had overhead protective cages installed on their tugs.
During transit, the support pad of the tail stand's central stabilizer, which was left in the down position, caught the lip of a manhole cover that extended 5/8" above the paved surface (Figures 2 and 3). This snag of the central stabilizer support pad on the edge of the manhole cover caused the tail stand to flip forward and strike the cargo handler in the head, neck, and back before pinning him to the steering wheel of the tug. The tail stand caused massive traumatic injuries to the cargo handler, who was pronounced dead at the hospital one hour later.
A fellow employee on site the night of the accident, who was interviewed by the Occupational Safety and Health Administration (OSHA) during their investigation, reported that approximately one hour before the fatal incident another tail stand in use on the site was damaged when the central stabilizer was left in the down position and caught on the same slightly raised manhole cover. However, the tail stand did not tip over and corrective action was not taken at that time. Police detectives investigating this fatality reported that the tail stand involved in this fatality also exhibited pre-existing visible wear and past repairs, indicating that the tail stand had been damaged previously. One detective reported that tail stands in use in this area of the airport are "all dinged up and dented." However, employees interviewed by OSHA and NJDHSS investigators reported that although the tail stands get damaged, they have never seen a tail stand tip over before.
It is notable that the cargo tugs used by another cargo handling company at this airport had overhead protective cages, whereas the tug involved in the fatal incident did not have this protective device installed. Also, worker interviews conducted by OSHA during their investigation revealed that the employee safety training was not comprehensive or cohesive, and employee awareness of safety was limited. Worker interviews also indicate that employees unfamiliar with certain pieces of equipment may still have access to, and be required to handle and utilize, that equipment.
![]() |
Figure 1: Tail stand and cargo tug |
![]() |
Figure 2: Close-up of central stabilizer support pad in down position |
![]() |
![]() |
Figure 3: Manhole cover contacted by central stabilizer support pad during transport |
Back to Top
Recommendations/Discussion
Recommendation #1: Airport vehicular tugs should be equipped with adequate overhead protective cages to prevent injuries caused by strikes from objects falling from above.
Discussion: Protective cages serve to stop or deflect objects from above falling onto the driver, which could potentially result in injury. A great deal of the loading and unloading of cargo at this airport involves lifting or lowering heavy items from overhead storage locations. Employees interviewed during the investigation reported that falling objects are a fairly common experience at this worksite, especially because items tend to shift during flight. In addition, overhead protective cages were commonplace on tugs used by other cargo moving companies at the airport. It is believed that if the decedent was using a tug that had an overhead protective cage, the weight of the falling tail stand would have been significantly deflected and therefore may have prevented this fatality.
Recommendation #2: Employees assigned to move and handle tail stands, as well as other large equipment, should receive detailed training on the potential hazards and safe work practices associated with these tasks.
Discussion:Initial and frequent refresher training should be provided to all employees who handle cargo and tail stands. Trained employees should demonstrate proficiency in handling large equipment and this should be documented. Only employees with training should be permitted to work with tail stands. In particular, employees must know that the central stabilizer of a tail stand must be in the up position, as per the manufacturer's instructions, before moving the tail stand because of the potential for the support pad to catch on an uneven or protruding surface. Also, employees must be aware that the head jaw strut (i.e. the upper support of the tail stand) must be fully lowered before movement, as per the manufacturer's instructions, because leaving this in an extended position can change the center of gravity of the tail stand and make it more likely to tip over.
Recommendation #3: Signage reminding crew members about important safe handling practices, such as raising the central stabilizer of the tail stand before attempting to move it, should be clearly visible. The warning labels should be prominent and clearly convey the seriousness of the hazard.
Discussion:The tail stand involved in this incident had a small warning label located near the front of the tail stand. The warning label read, "Caution: Center support pad must be fully raised before towing." This small warning label was not particularly notable and did not convey the seriousness of the hazard. Therefore, this warning label did little to motivate workers to change their behavior. Warning labels must provide enough information to generate interest and motivation among workers so that their warnings are heeded.
Recommendation #4: Employees must be given the appropriate amount of time to perform tasks required for successful completion of their job duties.
Discussion: Adequate staffing levels should be provided for loading and offloading cargo, and for other time-sensitive tasks. The employer should have effective plans to address staffing shortages, such as the ability to acquire trained staff on short notice through the use of "floating" shift employees. If employees perform overtime work, the employer should ensure that they are able to remain alert enough to perform tasks correctly and safely. OSHA and NJDHSS investigators were told by employees that, on the night of the accident, they felt rushed and the employer's attorney reported to OSHA and NJDHSS investigators that on the evening of the accident the ground crew was short-staffed by one employee.
Recommendation #5: Maintenance records for heavy equipment must be reviewed frequently. If repeat incidents or problems are noted, corrective action must be taken in order to correct equipment damage that could lead to injuries of employees.
Discussion: Based on the interviews and inspection of the tail stand by OSHA and the Port Authority, it was determined that a significant amount of damage had occurred over time to the tail stand. The Port Authority included in their report the results of an independent engineering assessment of the damaged tail stand. The fact that another tail stand was out of service due to a similar mishap an hour before the fatality strongly indicates the need to understand that significant damage to equipment can also lead to potential injury risks to employees.
Recommendation #6: Safety devices for aircraft tail stands that prevent movement of the stand unless the central stabilizer is in the correct position should be designed and integrated into the construction of the tail stand.
Discussion: Engineering controls, such as those described by this recommendation, are the most preferred method for controlling hazards. The lifting of the central stabilizer to the correct position would be required to move the tail stand if this engineering control was incorporated into the design of the tail stand. This would prevent injury because it would ensure that the operator utilized the tail stand correctly. The principal cause of this fatal accident could have been avoided by requiring the central stabilizer to be raised before the tail stand could be moved.
Recommendation #7: Employees should discuss, and management should actively seek, information related to potential problems or near-misses encountered by employees while performing work tasks. All near-misses should be carefully evaluated and preventive actions should be taken.
Discussion: Near-misses are important predictors of fatal accidents and serious injuries. Therefore, standard safety practice dictates that all near-misses should be evaluated and corrective action should be taken to avoid injury and death. In this case, the fatal incident could have potentially been avoided if the tail stand snag that occurred an hour before this fatal accident was assessed and corrective action was taken.
Appendix
Recommended Resources
It is essential that employers obtain accurate information on health, safety, and applicable OSHA standards. NJ FACE recommends the following sources of information which can help both employers and employees:
U.S. Department of Labor, Occupational Safety & Health Administration (OSHA)
Federal OSHA will provide information on safety and health standards on request. OSHA has four area offices in New Jersey that cover the following counties:
Hunterdon, Middlesex, Somerset, Union, and Warren counties
Telephone: (732) 750-3270
Essex, Hudson, Morris, and Sussex counties
Telephone: (973) 263-1003
Bergen and Passaic counties
Telephone: (201) 288-1700
Atlantic, Burlington, Cape May, Camden, Cumberland, Gloucester, Mercer, Monmouth, Ocean, and Salem counties
Telephone: (856) 757-5181
Federal OSHA
Web site: https://www.osha.gov/
New Jersey Public Employees Occupational Safety and Health (PEOSH) Program
The PEOSH Act covers all NJ state, county, and municipal employees. Two state departments administer the act; the NJ Department of Labor and Workforce Development (NJDLWD), which investigates safety hazards, and the NJ Department of Health and Senior Services (NJDHSS), which investigates health hazards. PEOSH has information available that may also benefit private employers.
NJDLWD, Office of Public Employees Safety
Telephone: (609) 633-3896
Web site: http://lwd.dol.state.nj.us/lsse/employer/Public_Employees_OSH.html
NJDHSS, Public Employees Occupational Safety & Health Program
Telephone: (609) 984-1863
Web site: http://www.nj.gov/health/peosh
On-site Consultation for Public Employers
Telephone: (609) 984-1863(health) or (609) 633-2587(safety)
Web site: www.state.nj.us/health/eoh/peoshweb/peoshcon.htm
New Jersey Department of Labor and Workforce Development, Occupational Safety and Health On-Site Consultation Program
This program provides free advice to private businesses on improving safety and health in the workplace and complying with OSHA standards.
Telephone: (609) 984-0785
Web site:
http://lwd.dol.state.nj.us/labor/lsse/employer/
Occupational_Safety_and_Health_Onsite_Consultation_Program.html
New Jersey State Safety Council
The NJ State Safety Council provides a variety of courses on work-related safety. There is a charge for the seminars.
Telephone: (908) 272-7712.
Web site: http://www.njsafety.org
Internet Resources
Other useful internet sites for occupational safety and health information:
- CDC/NIOSH - https://www.cdc.gov/niosh/
- Employment Laws Assistance for Workers and Small Businesses - http://www.dol.gov/elaws/
- National Safety Council - http://www.nsc.org/Pages/Home.aspx (Link updated 8/14/2012)
- NJDHSS FACE reports - http://www.nj.gov/health/surv/face/index.shtml
- CDC/NIOSH FACE - https://www.cdc.gov/niosh/face/
Reference
- Job Hazard Analysis. US Department of Labor Publication # OSHA-3071, 1998 (revised). USDOL, OSHA/OICA Publications, PO Box 37535, Washington DC 20013-7535.
New Jersey FACE Program
Fatality Assessment and Control Evaluation (FACE) ProjectInvestigation #07-NJ-038
Staff members of the New Jersey Department of Health and Senior Services, Occupational Health Service, perform FACE investigations when there is a report of a targeted work-related fatal injury. The goal of FACE is to prevent fatal work-related injuries by studying the work environment, the worker, the task, the tools the worker was using, the energy exchange resulting in the fatal injury, and the role of management in controlling how these factors interact. FACE gathers information from multiple sources that may include interviews of employers, workers, and other investigators; examination of the fatality site and related equipment; and reviewing OSHA, police, and medical examiner reports, employer safety procedures, and training plans. The FACE program does not determine fault or place blame on employers or individual workers. Findings are summarized in narrative investigation reports that include recommendations for preventing similar events. All names and other identifiers are removed from FACE reports and other data to protect the confidentiality of those who participate in the program.
NIOSH-funded state-based FACE Programs include: California, Iowa, Kentucky, Massachusetts, Michigan, New Jersey, New York, Oregon, and Washington. Please visit the NJ FACE website at www.state.nj.us/health/eoh/survweb/face.htm or the CDC/NIOSH FACE website at www.cdc.gov/niosh/face for more information.
The NJ FACE Project is supported by Cooperative Agreement #1 U60 OH0345-01 from the Centers for Disease Control and Prevention (CDC). The contents of this report are solely the responsibility of the authors and do not necessarily represent the official views of the CDC.
To contact New Jersey State FACE program personnel regarding State-based FACE reports, please use information listed on the Contact Sheet on the NIOSH FACE web site. Please contact In-house FACE program personnel regarding In-house FACE reports and to gain assistance when State-FACE program personnel cannot be reached.
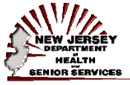
- Page last reviewed: November 18, 2015
- Page last updated: October 15, 2014
- Content source:
- National Institute for Occupational Safety and Health Division of Safety Research