69-Year-Old Sanitation Worker Run Over by Refuse Truck
New Jersey Case Report: 08NJ079
Report Date: March 10, 2010
Summary
On October 17, 2008, a 69-year-old male private sector sanitation worker died after he was run over by a refuse truck. On the day of the incident, the victim and one other worker were collecting tree brush in a rural southern New Jersey community. The workers had stopped the rear-loading compaction truck and began to load brush into the rear compartment. Soon after initiating the compaction cycle of the truck, the vehicle began to move, uncontrolled, in a forward direction. Both workers immediately ran after the vehicle, and the decedent fell under the truck and was crushed to death. NJ FACE investigators recommend that these safety guidelines be followed to prevent similar incidents:
- Sanitation workers should be trained on the safe procedures for operating and loading sanitation trucks, including auxiliary compactor equipment.
- Sanitation truck drivers should not leave the vehicle unless needed as a spotter; in which case, the gear shift should be set to "neutral" and the emergency brakes engaged.
- Equipment should be in good working order, and safety interlocks or other control mechanisms should never be modified, disconnected, or disengaged.
- A safety and health plan based on a job hazard analysis should be developed by the employer and followed for each trash route.
Introduction
On October 17, 2008, a Federal OSHA compliance officer notified NJ FACE staff of the death of a 69-year-old worker who was killed after being run over by a rear-loading compactor refuse truck. A NJ FACE investigator contacted the employer and arranged to conduct an investigation, which took place on October 22, 2008. During the visit, the NJ FACE investigator interviewed the immediate supervisor and colleagues of the decedent. Additional information was obtained from the medical examiner's report, death certificate, and employer incident summary.
The company that employed the decedent was a trash collection and trucking company that collected trash once per week, and tree brush once every two weeks. The victim had many years of experience in the waste collection industry; at the time of the incident he was retired and working part time. He was a member of the local union prior to retirement, and the other worker was a current member. Employee training, including health and safety training, was conducted on the job by the employer.
Back to Top
Investigation
The incident occurred on a clear October day (approximately 65oF, no wind). A two-person crew was assigned to collect brush for a rural southern New Jersey township. The decedent was functioning as the driver, and the other worker (the "helper") rode in the passenger seat until arrival at a pick-up point. The truck they were operating was a 300-horsepower, rear-loading, compactor refuse recycling truck. The route was a one-load route; that is, they only filled the truck once during the day; no mid-route dumping was conducted.
The workers left the yard where the truck was stored at 6:00 am that morning. The workers arrived at the assigned route in approximately 45 minutes. A few streets into the collection, the truck pulled up to a stop near a curb to load brush into the compaction unit. The helper, who was usually on the truck, chose to walk behind the truck from the previous stop. The decedent stopped the truck facing the next stop, which was northbound on the left side of the road. (see Figures 1 and 2). He then exited the truck to assist with the load. While the two workers were loading the brush, the helper activated the "speed-up button," which triggers the engine to run faster (at approximately 2,000 rpm) to power the hydraulic system of the load compactor, which crushes and compacts the load (see Figure 3). As soon as the button was pushed, the truck unexpectedly started moving forward, traveling northbound. Both workers ran to catch up to the truck; the decedent ran along the driver side between the truck and the curb, and the helper ran along the passenger side. The helper was able to catch up to the vehicle and hit the speed-up button which slowed the truck’s movement. The helper reached the passenger-side door and managed to enter the cab and fully stop the truck. He then exited the cab, looked around on the other side of the vehicle for the decedent, and saw that he had been crushed by the driver’s side wheels. The truck had moved approximately 50 feet north through an intersection with traffic lights. No one else was injured.
Back to Top
Recommendations/Discussion
Recommendation #1: Sanitation workers should be trained on the safe procedures for operating and loading sanitation trucks, including auxiliary compactor equipment.
Discussion: Training is a critical aspect of the prevention of injuries in any potentially hazardous working condition. Many of these conditions are evident in the waste collection industry, including struck-by, crushing, and fall hazards. In NJ, since 1991, there have been 25 workers killed while working on or near sanitation trucks, and many nonfatal injuries. Training can help combat these risks, and there are already many educational materials that address this industry, including the following:
- NIOSH, Preventing Worker Injuries and Deaths From Moving Refuse Collection Vehicles; available at: https://www.cdc.gov/niosh/docs/97-110/ (Link updated 4/13/2015)
- NJDHSS, Don't Get Hurt Working Around Sanitation Trucks; available at: http://www.state.nj.us/health/surv/documents/sanwk_en.pdf
Recommendation #2: Sanitation truck drivers should not leave the vehicle unless needed as a spotter; in which case, the gear shift should be set to "neutral" and the emergency brakes engaged.
Discussion:
In this case, the driver left the vehicle to assist with the loading of brush and left the truck running, which is necessary in order for the hydraulic system to operate. It is not clear whether or not the emergency brakes had been engaged. Accident investigators tested the brakes on the day of the incident, and the brakes failed. However, the standard procedure for operators is to remain in the vehicle during collection activities when the vehicle is in gear and when compaction equipment is operating. If the operator should exit the vehicle, it should be put in "neutral" with the emergency brake engaged.
Recommendation # 3: Equipment should be in good working order, and safety interlocks or other control mechanisms should never be modified, disconnected, or disengaged.
Discussion: The particular model of truck involved in this incident had the neutral relay removed and the "speed-up" button was converted to a toggle switch. A properly working neutral relay prevents the compactor cycle to be activated while the vehicle is in "drive." The compactor cycle was therefore able to be engaged while the truck was moving from stop-to-stop. The speed-up button, which activates the compactor, was designed by the manufacturer to activate one full compaction cycle. In this incident, the modifications to the compactor enabled it to be started and stopped at any time.
These two alterations compromised the safety of the equipment. As per ANSI Z245.1, Section 6.2.1 (j), "No one should disable or bypass safety equipment or other protective devices," and "Mobile equipment must not be operated unless these devices are fully functional."
Recommendation #4: A safety and health plan based on a job hazard analysis should be developed by the employer and followed for each trash route.
Discussion: Employers should conduct a job hazard analysis, with the participation of employees, of all work areas and job tasks. A job hazard analysis should begin by reviewing the work activities for which the employee is responsible, and the equipment that is needed. Each task is further examined for mechanical, electrical, chemical, or any other hazard the worker may encounter. A source of information on conducting a job hazard analysis is included in the Appendix.
![]() |
![]() |
![]() |
FIGURE 3. “Speed-up” button located on side of rear-loading unit. |
Appendix
Recommended Resources
It is essential that employers obtain accurate information on health, safety, and applicable OSHA standards. NJ FACE recommends the following sources of information which can help both employers and employees:
U.S. Department of Labor, Occupational Safety & Health Administration (OSHA)
Federal OSHA will provide information on safety and health standards on request. OSHA has four area offices in New Jersey that cover the following counties:
Hunterdon, Middlesex, Somerset, Union, and Warren counties
Telephone: (732) 750-3270
Essex, Hudson, Morris, and Sussex counties
Telephone: (973) 263-1003
Bergen and Passaic counties
Telephone: (201) 288-1700
Atlantic, Burlington, Cape May, Camden, Cumberland, Gloucester, Mercer, Monmouth, Ocean, and Salem counties
Telephone: (856) 757-5181
Federal OSHA
Web site: https://www.osha.gov/
New Jersey Public Employees Occupational Safety and Health (PEOSH) Program
The PEOSH Act covers all NJ state, county, and municipal employees. Two state departments administer the act; the NJ Department of Labor and Workforce Development (NJDLWD), which investigates safety hazards, and the NJ Department of Health and Senior Services (NJDHSS), which investigates health hazards. PEOSH has information available that may also benefit private employers.
NJDLWD, Office of Public Employees Safety
Telephone: (609) 633-3896
Web site: http://lwd.dol.state.nj.us/lsse/employer/Public_Employees_OSH.html
NJDHSS, Public Employees Occupational Safety & Health Program
Telephone: (609) 984-1863
Web site: http://www.nj.gov/health/peosh
On-site Consultation for Public Employers
Telephone: (609) 984-1863(health) or (609) 633-2587(safety)
Web site: www.state.nj.us/health/eoh/peoshweb/peoshcon.htm
New Jersey Department of Labor and Workforce Development, Occupational Safety and Health On-Site Consultation Program
This program provides free advice to private businesses on improving safety and health in the workplace and complying with OSHA standards.
Telephone: (609) 984-0785
Web site:
http://lwd.dol.state.nj.us/labor/lsse/employer/
Occupational_Safety_and_Health_Onsite_Consultation_Program.html
New Jersey State Safety Council
The NJ State Safety Council provides a variety of courses on work-related safety. There is a charge for the seminars.
Telephone: (908) 272-7712.
Web site: http://www.njsafety.org
Internet Resources
Other useful internet sites for occupational safety and health information:
- CDC/NIOSH - https://www.cdc.gov/niosh/
- Employment Laws Assistance for Workers and Small Businesses - http://www.dol.gov/elaws/
- National Safety Council - http://www.nsc.org/Pages/Home.aspx (Link updated 8/14/2012)
- NJDHSS FACE reports - http://www.nj.gov/health/surv/face/index.shtml
- CDC/NIOSH FACE - https://www.cdc.gov/niosh/face/
Reference
- Job Hazard Analysis. US Department of Labor Publication # OSHA-3071, 1998 (revised). USDOL, OSHA/OICA Publications, PO Box 37535, Washington DC 20013-7535.
- ANSI Z245.1: Mobile Wastes and Recyclable Materials Collection, Transportation and Compaction Equipment - Safety Requirements.
New Jersey FACE Program
Fatality Assessment and Control Evaluation (FACE) ProjectInvestigation #08-NJ-079
Staff members of the New Jersey Department of Health and Senior Services, Occupational Health Service, perform FACE investigations when there is a report of a targeted work-related fatal injury. The goal of FACE is to prevent fatal work-related injuries by studying the work environment, the worker, the task, the tools the worker was using, the energy exchange resulting in the fatal injury, and the role of management in controlling how these factors interact. FACE gathers information from multiple sources that may include interviews of employers, workers, and other investigators; examination of the fatality site and related equipment; and reviewing OSHA, police, and medical examiner reports, employer safety procedures, and training plans. The FACE program does not determine fault or place blame on employers or individual workers. Findings are summarized in narrative investigation reports that include recommendations for preventing similar events. All names and other identifiers are removed from FACE reports and other data to protect the confidentiality of those who participate in the program.
NIOSH-funded state-based FACE Programs include: California, Iowa, Kentucky, Massachusetts, Michigan, New Jersey, New York, Oregon, and Washington. Please visit the NJ FACE website at www.state.nj.us/health/eoh/survweb/face.htm or the CDC/NIOSH FACE website at www.cdc.gov/niosh/face for more information.
The NJ FACE Project is supported by Cooperative Agreement #1 U60 OH0345-01 from the Centers for Disease Control and Prevention (CDC). The contents of this report are solely the responsibility of the authors and do not necessarily represent the official views of the CDC.
To contact New Jersey State FACE program personnel regarding State-based FACE reports, please use information listed on the Contact Sheet on the NIOSH FACE web site. Please contact In-house FACE program personnel regarding In-house FACE reports and to gain assistance when State-FACE program personnel cannot be reached.
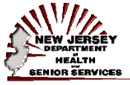
- Page last reviewed: November 18, 2015
- Page last updated: October 15, 2014
- Content source:
- National Institute for Occupational Safety and Health Division of Safety Research