Two Teen Workers Asphyxiate in an Agricultural Silo
Washington Case Report 03WA038
Release Date: March 31, 2008
Summary
In August of 2003, two 16-year-old farm workers died when they were asphyxiated in an oxygen-limiting silo. The two young men were in the process of helping a silo dealer/distributor service representative conduct maintenance in the silo when the incident happened. There were no witnesses to the event, as the silo representative left the site temporarily during the time of the incident, and the other farm workers, including the farm owners, were working elsewhere on the farm site. The two victims were discovered unconscious inside the 90-foot silo shortly after the silo representative had returned to the farm. The farm owner, as soon as he learned that the two young workers were unresponsive in the silo, attempted to rescue them. Emergency medical persons were called and responded to the incident. Both of the victims died at the scene. Physical rescue and emergency response was hampered by having untrained persons attempting a confined space rescue at height, and the time-lag of the rescue personnels’ arrival at the site.
To prevent similar occurrences, the Washington State Fatality Assessment & Control Evaluation (FACE) Investigative team concluded that employers working on farms and/or other operations that work with silos and confined spaces should follow these recommendations:
- Employers should have a detailed confined space entry plan in place for all confined spaces.
- Employers should review and use alternative methods so that confined space entry is not required.
- Employers should consider contacting external expert consultants/contractors to help with confined space management and confined space entry processes.
- Employers and contractors need to follow manufacturers’ recommended maintenance procedures.
- Employers need to have processes in place that prevent unauthorized entry.
- Employers need to maintain close supervision of all teen employees and contractors.
- All permit-required confined spaces must have detailed rescue processes and personnel in place.
Introduction
In August of 2003, the Washington State FACE Program was notified by WISHA* (Washington Industrial Safety & Health Administration) (now known as DOSH, Division of Occupational Safety & Health), of the death of two 16 -year-old male farm workers. The two victims died in a confined space incident in a farm silo located in eastern Washington state.
The Washington FACE Field Investigation team met with the regional WISHA representative assigned to this case. The incident was carefully reviewed with the WISHA Compliance Officer who provided valuable insight related to the incident, based on their investigation.
After waiting for a reasonable period of time, the FACE Field Investigator contacted the farm owners who graciously allowed the FACE team to visit the farm and the incident site.
The two young victims were working on a small family dairy farm, consisting of approximately 200 head of dairy cattle. The farm’s primary product was the production of milk that was sold through a cooperative dairy products organization. The farm also grew hay, which was used for dairy cattle feed. The hay was stored in silos and other storage formats at the farm.
The daily farm work activities were performed by the farm owners, family members and by several employees who worked regularly for the farm. On occasion, the farm would hire part-time temporary help to fill with seasonal or other work coverage needs.
Both victims were 16-year-old male high school students. One of the victims was a family member (son) of the farm owners and the other 16-year-old was a close friend of the first victim and of the farm family.
The young men worked various jobs and projects on the farm, some of which were routine tasks such as helping with the irrigation system for the hay fields and others as needed, such as being helpers for the silo maintenance project discussed in this investigation report.
The work activity for each of the boys was determined by the farm owner who set up assignments for the victims on a regular basis. Both of the victims were experienced at doing a variety of farm work but had minimal experience in working on or in silos.
The 16-year-old farm owner’s son and friend had worked on the farm together for a while and both were very comfortable with farm work, and eagerly took on a variety of tasks that were presented to them. The young family friend had helped out at the farm for a couple of years, working during the summer, and on a part-time basis while school was in session. Both of the young men worked varying hours per day depending on need and availability. The hours were modified when they attended school, and they worked more hours during the summer months when school was not in session.
According to the farm owner, whenever there was any work to be done with the silos, the two victims had worked with the owner on only a few occasions helping with the loading of the silo and other set-up activities. But they only worked under direct supervision of the farmer on each of those occasions. He had told the two young men many times that they were never to work on the silos on their own.
The farm had no written safety program and no confined space entry process or procedure in place nor did they provide any formal safety training. They did have a non-structured “on-the-job” training/instruction process as many small farms have. Training is passed along through experience and “generational” learning developed within the farm community.
On the incident date, the two young men had just started work on an August summer morning. They were asked to work with a silo dealer/representative to help prep one of the farm silos for maintenance work scheduled to be done that day. The farmer did mention that he emphasized safety for all the jobs workers performed on the farm. They had actually stopped entries into the farms silos some years ago for fear of the hazards of the feed stock “bridging” and collapsing in the silos, where it could entrap the worker.
The farmer indicated that they had provided on-the-job training for the two young men and the training was complemented by direct supervision, coupled with visual observation until the farmer felt comfortable that the victims could perform assigned tasks with minimal supervision.
The farm had a total of four Harvestore® silos located within the farm complex. The incident site for this FACE investigation was one of two Harvestore® silos that were situated adjacent to each other located on the southeastern portion of the farm property.
The farm owners had contacted an area silo dealer/representative earlier that year to arrange for the installation of a manure waste sludge tank that the farm had purchased. The farm owner had also ordered replacement breather bags and wanted to have them installed while the silos were full with haylage (stored hay). The farm had worked with this same dealer/representative on occasion over the past 6 -10 years, dealing with a variety of other farm relate issues, but this was the first time they were doing any work on the silos.
The plan in place for the silo maintenance project was to replace the Harvestore® breather bags in one of the silos. The farm had installed its first Harvestore® sometime in 1965 and the others in the early 1970’s, all under the direction of the current farm owner’s father.
Breather bags are a unique component of the Harvestore® “Oxygen deficient” or oxygen limiting silos. Breather bags are designed to manage the space on the top of the silos so that it preserves the anaerobic (oxygen free) conditions in the head space of the silo, while allowing air to expand and contract with temperature changes. One of the main characteristics of an oxygen deficient silo is to minimize contact of air (more specifically oxygen) with stored feed in the silo. The breather bags act as pressure sacks to keep oxygen out of the silo. The idea is air flowing in and out of breather bags does not come in contact with stored feed.
The Harvestore® silos are also constructed with other design features such as steel sheets coated with fused glass that are put together with special sealants, rubber-like gaskets and marine-type doors and hatches that work in concert with each other to help minimize oxygen exposure to feed stored in the silo.
The manufacturer recommends that the breather bags be inspected on a regular basis and replaced periodically to maintain the integrity of the oxygen limiting characteristics of the silo and thus the integrity of the feed that is stored in them.
The current farm owner noted that he was having some problem with the haylage feed quality and subsequently discovered that one of the breather bags was torn. This was an original breather bag from 1972.
The farmer had ordered replacement bags during the previous summer, but the service representative requested that the job be delayed until late summer of 2003 because of a scheduling conflict. The silo dealer/representative was to be on-site the previous week to perform the breather bag change-out but that did not happen and the operation was moved to the following Tuesday.
The owner/farmer would have been able to work with the silo dealer/representative on that Monday but since it had been moved to Tuesday, he needed work with a silage bagger that he had borrowed to store additional hay. So on Tuesday, the two 16-year-olds were asked to assist the silo dealer/representative work on the breather bag change-out.
Prior to the silo dealer’s arrival the two young men were to move sprinklers, an activity they would routinely have done on a normal day, but when the silo dealer arrived they were to switch their activities to whatever they could do to help with the replacement of the silo breather bags.
On that Tuesday morning, the farm owner saw the silo dealer/representative’s truck down near the Harvestore ® silo that they were planning to work on, so he sent the two young men to interact with the silo representative. Shortly after the two 16-year-olds made contact with the silo representative, the representative noticed that he did not have all the rope and other material that was needed for the breather bag replacement.
He left the farm to go to a nearby town, which was about 30 minutes away, to pick up the needed rope and equipment.
When the silo dealer returned about an hour and a half later that morning, he did not see the two 16-year-olds anywhere around the two silos. He saw that the top hatches of the silo were open that he was going to work on, so he climbed up the silo and to his shock, found both of the young men lying inside the silo. They were unresponsive to his shouts.
He climbed back down off the top of the silo and went to get the farm owner. As soon as the farmer arrived at the silo he noted that the tractor and the PTO were not connected to the blower. The farmer quickly set up the blower/ventilation system to get fresh air into the silo. The farmer sent the service representative to get additional help and bring them back to the silo. Calls to 911 were attempted but they were not able to get a cell phone signal.
Other farm workers arrived at the scene, and sometime during this sequence of events as more help was arriving, someone was able to get a call out to 911. Local area volunteer fire and emergency teams responded to the 911 call. Entry and rescue attempts into the silo were found to be very complicated and difficult. They were not very well prepared to conduct either a confined space rescue, or a rescue from a 90-foot silo.
After emergency service personnel arrived and evaluated the situation, it was determined that the victims had expired and the emergency was now a recovery and not a rescue process. The coroner’s office listed the time of death for the two young men at 9:25AM. The time of death was approximately 5 minutes before the first 911 call was made.
* The OSHA State Plan program in Washington State.
Back to Top
Investigation
On a Monday morning in August of 2003, two young men (the 16-year-old victims) were working on a small family farm in eastern Washington. They were up early to address the many tasks that were needed to be done on a small farm operation.
Both victims were high school students. One of the victims was the son of the farm owners and other was a close friend of the family.
On the incident morning while the farm family, (including the two victims), were having breakfast, they noticed the silo dealer / representative’s pick-up truck parked near the Harvestore® silos that were in view from the kitchen table.
The farm owner asked the two 16-year-olds to go down to the silos and check-up on the silo dealer. The farm owner had other work that he needed to attend to that morning but planned on checking-in with the silo representative throughout the day as work progressed.
One of the tasks they were assigned to do that day was to help with the silo setup and provide other assistance as necessary for the replacement of breather bags on one of the several Harvestore® silos located on the farm.
The silo breather bag replacement project process started about a year prior to the incident when the farmer ordered the replacement breather bags. He had made arrangements with an area service representative to have breather bags installed during the summer of 2003.
The farm owner had determined on that previous summer, that there was a need to replace one or more of the breather bags that was used in this type of silo.
There were two Harvestore® silos adjacent to each other at the incident site location. They were both oxygen-limiting silos. Both silos were 90 feet in height and were constructed of rolled sheet steel curved plates. The Harvestore® manufacturer uses a fused-glass coating on both sides of the steel which is designed to resist acids from fermented stored feeds.
The fatal incident silo (silo #1) was slightly larger than the adjacent silo (silo #2). Silo #1 was 25 feet in diameter, while silo #2 was 20 feet in diameter. Both of these Harvestore® silos were built in place in the 1970’s.
They each had 3 marine-type hatches on top of the domed “roof” of the silo. There was a center hatch which lines up with a feed chute that would be positioned to deliver hay into the silo. There were two other hatches situated near the sides of the silo “roof”. They were used as maintenance openings. One of the two hatches, the one closest to the silo ladder access-way, would be opened during filling to release pressure and allow for more efficient loading.
The farm owner contacted an independent Harvestore® dealer / distributor who he had worked with the farm for past several years, to start work on the breather bag replacement process.
The silo representative/farm equipment dealer was in communication with the farm owner on the week prior to the incident. He had been working with the farm on the preparation and the installation of a new slurry holding tank for the dairy cattle manure/waste materials. The farm owner at that same time wanted to replace the breather bags on one of the Harvestore® silos.
The farm owner had purchased the breather bags the year before from the silo representative/farm equipment dealer, and then looked for an opportune time during their farm operation schedule to replace them which was during a time when they were cutting and storing hay for the fall and winter months.
The silo representative had told the farm owner that the “best” way to replace the breather bags was to have the silo full so they could stand on top of the hay. This was they way the silo representative had changed out breather bags in other silos in the past.
On the Friday prior to the fatal incident, the farmer worked with the two 16-year-olds to prep the silo for entry in order to facilitate the removal of the old breather bags and replace them with the new breather bags that the farmer had purchased.
The silo service person was to be at the site on the following Monday to replace the breather bags, so they wanted to have the silo as full as possible to accommodate the breather bag replacement process.
As part of the farm’s normal silo filling operation, alfalfa hay is dried and shredded, and is blown into the top of the silo. The farmer would position a tractor near the silo, and use a PTO (power take-off) unit that would be attached to a fixed blower (or transportable blower) located near the base of the silo.
The blower would then have hay fed into the system and the blower (via air pressure), would in turn force the hay up through a pipe, and on up to a feed chute located at the top of the silo. The feed chute would then funnel the hay into the silo.
On the Friday before the incident, the farmer closely supervised the two young men in the silo filling operation. The farmer climbed the attached silo ladder to the top and opened the center feed hatch of the silo and one of the maintenance hatches. He then set up the tractor PTO / blower unit and delivered hay to the top of the silo. As part of this process, the farmer also used the blower to ventilate the silo for entry as needed.
The two young men also climbed up to the top of the silo several times to look into the top hatches to check the level of the hay in the silo. When the hay was near the top, the farmer supervised the two boys as they entered through the open maintenance hatch at the top and climbed down onto the hay in the silo.
As hay is fed into the silo through the center hatch, it has the natural tendency to build up more in the center in the shape of a cone, with less hay on the edges. The two young men would move the hay from the center hatch, where it was being blown in, over to the edges and then level and compact the hay in order to get as much hay into the silo as possible. They would then have it ready to stand on with as firm a footing as they could to be able work on the breather bag replacement. The farmer stayed at the base of the silo to operate the blower and to feed the hay into the system.
One of the problems the farmer was having during this same time frame, was the hay unloader system for the adjacent silo (silo #2), was not working and thus was inoperable.
This meant that they had to draw the haylage from the bottom of the silo (silo #1) that they were currently filling to use in their daily cattle feeding process.
This also meant that they would need to add more hay to silo #1 prior to the upcoming Monday to accommodate the breather bag replacement. The goal was to fill the silo as full as possible on that Friday so they would not have to spend as much time on Monday adding more hay to silo #1, and thus have the silo ready when the silo service representative arrived to replace the breather bags.
Because they were still not able to get the second silo (silo #2) unloader working, they decided to also fill silo #1once again on that Saturday. A cousin of the 16-year-old friend helped with the silo filling on that Saturday. They fed hay into the silo until it reached a level of about three feet from the top of the center hatch of the silo and then stopped.
Once filled, they sealed the hatches, and went on to work on other activities on the farm. The Saturday silo filling process was coordinated and totally supervised by the farmer.
When Monday came around, the farmer was prepared to work with the silo representative but the representative did not make it to the farm on that day so the silo remained sealed.
On that Tuesday, the farmer needed to work with a silage bagger that the farmer had borrowed from another farm. The bagger stored additional hay within a horizontal storage system on the ground. He needed to get the borrowed bagger back to the other farm as soon as possible, and since the second silo unloader was not working he was not able to add more hay to the second silo (silo #2).
The farmer had instructed the two 16-year-olds to move sprinklers that morning until the service representative arrived and then they should go help the service representative with the breather bag replacement.
The silo service representative arrived sometime around 7:30 AM that Tuesday morning. The service representative did not announce his arrival to the farmer but drove directly to the silo that he was going to be working on that day. There was no discussion or co-ordination of activity between the farmer and the service representative on that morning.
The farmer happened to see the service representative’s pickup truck parked by the two Harvestore silos that morning and sent the two 16-year-olds to the silo site, while the farmer prepared to work with the silage bagger at another location on the farm.
As the silo service representative was setting up his equipment for the breather bag replacement, he discovered that he had forgotten rope and pipe clamps that he needed to do the job. The service representative said he got directions from the two 16-year-olds to go to a store in the nearest town and he left the farm site somewhere around 8:00 AM.
It was noted from employee interviews, that at about 8:30 that morning, after one of the farm workers had dropped a tractor off at a shed near the silos, the worker had heard the two 16-year-old boys talking but he could not make out what they were saying and did not witness what the young men were doing. The farm worker than left the area and went to his house which was located nearby.
It was determined during the course of the investigation, using the store transaction date and time on the receipt, that service representative made the purchases for the additional material needed for the silo breather bag replacement at 8:32 AM.
The farm worker, who had earlier gone to his house, was driving into town when he passed the service representative heading back to the farm. This was around 9:00 AM.
At around 8:40, the farmer, still working with the borrowed hay bagger at a location within sight of the silos, happened to notice that the silo fill chute had been repositioned. The silo chute had been pulled away from the hatch and secured in place. The farmer did not see the two young men nor did he see the service representative anywhere around the silos during this observation.
When the service rep returned to the farm, he once again parked his vehicle near the Harvestore® silo that he was going to work on. And just like the first time when he arrived at the site, he once again did not check in with the farm owner.
As the service representative was unloading his equipment, along with the newly purchased materials from his vehicle, he noted that he did not see either of the two young men that he was working with earlier in the morning.
The service representative decided to check the silo to see what first needed to be done for the breather bag replacement process. He grabbed the rope that he had just purchased and climbed the 90 foot silo using the external ladder that was attached to the side of the silo.
When he got to the top of the silo, he saw that both hatches were already open. He checked inside the open maintenance hatch which was the one closest to the silo ladder.
He noted that the hay level was about 12 feet below the top hatch and they would need to fill the silo with several more feet of hay in order to be able to stand in the silo to work on the breather bag replacement.
He next walked to the center hatch (the feed hatch), to check the level of hay at that location. He looked down through the silo hatch and to his alarm saw the two 16-year-olds both lying on their sides on top of the hay.
He started yelling at the boys to get their attention but they were unresponsive. The silo service representative then looked around to see if there might be other persons in the area that he could call for help. He did not see anyone around nor was there anyone responding to his subsequent shouts for help.
He quickly got down from the silo, got into his vehicle and drove to get help from the farm owner and / or any other farm workers that he could find.
The service representative was able to find the farm owner and they both rushed back to the silo. The first thing that the farmer noted was that the tractor and the PTO unit were not connected to the blower. He recognized that this was a serious problem.
The blower’s primary function is to feed hay into the silo using air pressure powered by the tractor’s PTO connection, but the farmer also used the blower mechanism to “blow fresh air” into the silo.
This was the way the farmer ventilated the silo whenever an entry was necessary. The farmer was very familiar with the fact that it was a very important part of the process that the silo be ventilated before anyone entered in through the top of the silo.
The farmer next sent the service representative to find the nearest farm employee(s) and have them hurry to the silo to help with this emergency situation. The farm owner was sure one worker was located at the farm milk house. The service representative went in that direction to get additional help.
The farmer in the meantime scrambled to the top of the silo. When he got to the top hatches, he noted that he could not stand near the hatches because the gases blowing up out of them were extremely bad. An attempt was made to call 911 but there was no cell phone signal available.
It was determined, via 911 records, that someone was able to get through to 911 at about 9:30 AM, to activate the 911 emergency response.
After letting the blower work for a few minutes (the actual time is unknown), the farmer prepared to lower himself down through the open hatch to where the two victims lay, using the rope the service representative had carried up to the top of the silo. The farmer was very much aware that the breathable air in the silo was still “bad” based on the odor evolving from the hatches, but felt confident that he would be “ok” entering the silo because the blower would provide enough “clean air” for the entry. This was based on the farmer’s previous experience of going into the silos in the past.
About this same time the service representative and one of the farm workers arrived back at the silo. The service representative and the farm worker climbed to the top of the silo and found that the farmer was getting ready to enter the silo to attend to the two 16-year-olds.
With the help of the service representative and the farm worker, the farmer lowered himself down into the silo. He immediately got a rope around the first victim that was directly under the center feed hatch. The service representative and the farm worker pulled the first victim out of the silo.
Outside emergency personnel began to arrive somewhere around 9:40 A.M. The situation was very chaotic as a number of persons were trying to assess the situation and as well as trying to understand what they needed to do to deal with this emergency.
There was considerable noise surrounding the incident site that added to the confusion and the urgency of the situation. The tractor was running to keep the blower going and people where yelling and scrambling around trying to find out what was going on, and vehicles and personnel were arriving in a continuous stream.
Almost all of the emergency responders were volunteers and none were familiar with confined space entry or high angle rescue.
At one point, someone turned the tractor engine off to cut down on the noise. The farmer immediately responded by having the tractor restarted. The tractor was providing vital ventilation to the silo during the rescue process.
There were also many responders who were climbing the silo ladder in order to check on what was happening and trying to determine how to help with the rescue.
At this point they were actually getting too many people gathering around this very limited space near the top of the silo and were creating secondary hazards to rescue people such as the possibility of someone falling off the silo and perhaps even overloading the top of the silo.
No one was wearing fall protection while climbing or working on the silo. No one was really sure what the safe loading for the top of the silo was. There was concern that the silo roof could collapse.
Several responders were also trying to provide CPR to the first victim who was lying on top of the silo, so room on top of the silo was at a premium. Many responders were asked to get down off of the silo and remain at ground level.
There was little to no organization in the process. The farmer, who was probably the most stressed of the rescuers also might have had the best perspective of what had to be done to facilitate the rescue, and provided some degree of direction for the rescuers during this very traumatic situation.
As rescuers were attending to the first victim, the farmer’s attention quickly focused on to the second victim. The second victim was lying off to the side, away from the center hatch and the farmer needed some help to position the second victim so he could be pulled through a silo hatch, again using a rope to assist in the process. The emergency team on top of the silo applied CPR to the second victim as soon as he was up and out of the silo hatch.
CPR was not successful for either of the two victims. There was a moment of stark realization that there was nothing else anyone could do to save these two young men.
The rescue team and the farmer now needed to focus on the next steps, the first of which was how to get everyone and the two young men down from the 90 foot silo safely.
A local business, situated only a couple of miles from the farm, provided a Stokes basket to help bring the boys down from the silo. They were also able to locate people with Nordic rescue expertise who helped with the rigging process.
The two young men, both 16 years of age, died in a very tragic and sobering confined space fatality incident on a family farm. The sad event not only strongly affected the local community, but it also affected many others throughout the state and beyond.
The farm owners, who were both family and friends of the victims most graciously agreed to assist the Washington FACE team help others, with the publication and communication of written safety materials designed to get the word out about the incident to the farm community, and to let them know how dangerous confined spaces can be and how unforgiving those spaces can be without taking extraordinary precautions for those who have a need to enter those spaces. The help from the farm owners is greatly appreciated.
Cause of Death
The coroner listed the cause of death (for both victims), as the result of asphyxia due to suffocating gases and chemicals in a silo.
Recommendations/Discussion
Recommendation #1: Employers should have a detailed confined space entry plan in place for all confined spaces.
Discussion: A typical farm can have a multitude of silos, storage structures, tanks, bins, pits and a variety of other compartments that could be classified as permit-required confined spaces.
Permit-required confined spaces have a long history of being involved in many serious injuries, illness, and deaths.
A permit-required confined space or permit space is a confined space that has one or more of the following characteristics capable of causing death or serious physical harm:
- Contains or has a potential to contain a hazardous atmosphere.
- Contains a material with the potential for engulfing someone who enters the space.
- Has an internal configuration that could allow someone entering to be trapped or asphyxiated by inwardly converging walls or by a floor, which slopes downward and tapers to a smaller cross-section.
- Contains any physical hazard. This includes any recognized health or safety hazards including engulfment in solid or liquid material, electrical shock, or moving parts.
- Contains any other recognized safety or health hazard that could either:
- Impair the ability to self rescue
or - Result in a situation that presents an immediate danger to life or health.
- Impair the ability to self rescue
The silo involved in this incident was a good example of a permit-required confined space. Because of the known and recognized hazards related to feed storage silos and in particular oxygen deficient silos, it is imperative that employers have a written and well defined confined space entry plan and entry process in place that utilize permit-required procedures. The permit process has to insure the safety of all entrants that may have a need to go into the confined space. The plan needs to be well orchestrated and have enough detail describing all elements of the entry procedure and permit process so that it is clearly understood by workers, contractors and service and maintenance people who have a need to work on, in, or around a confined space.
As an employer:
You must
Develop a written program, before employees enter, that describes the means, procedures, and practices you use for the safe entry of permit-required confined spaces.
Include the following when applicable to your confined space entry program:
- Documentation of permit entry procedures.
- Documentation used for alternate entry procedures.
- How to reclassify permit-required confined spaces to non-permit spaces.
- Designation of employee roles, such as entrants, attendants, entry supervisors, rescuers, or those who test or monitor the atmosphere in a permit-required space.
- Identification of designated employee duties.
- Training employees on their designated roles.
- How to identify and evaluate hazards.
- Use and maintenance of equipment.
- How to prevent unauthorized entry.
- How to coordinate entry with another employer.
- How to rescue entrants.
Training
Training is an essential element in helping recognize hazards associated with confined spaces. Not knowing the required elements of a permit-required confined space and not knowing the hazards of the confined space can lead to serious injury or even death.
- Provide training for each employee involved in permit-required confined space activities, so that they can acquire the understanding, knowledge and skills necessary to safely perform their assigned duties.
- All contractors and maintenance representatives need to be fully trained in confined space activities.
- Site specific training also must be done at the employer’s/customer’s site.
- Training might have helped prevent the loss of two young lives in this silo incident.
Monitoring
Testing and monitoring of a permit-required confined space atmosphere is a critical part of any confined space entry plan.
- The employer / contractor needs to have a process and equipment to evaluate the confined space prior to every entry.
- Testing should ensure that testing and monitoring is consistent with the hazards of the confined space.
- The evaluation of the confined space requires testing for the oxygen content, concentration of flammable contaminants and concentration of other potential harmful contaminants in the confined space.
- Entry into the space must not happen until monitoring has been completed and entry has been approved via the permit process.
- The silo manufacturer has a permanent warning on their silo hatches telling entrants to “Test Air Before Entering”.
- The space must have a safe level of oxygen before entry can be made into the confined space.
- Oxygen-limiting silos are designed to keep oxygen out of the silo to reduce the degradation of the feed stored in them and in doing so, create an oxygen deficient atmosphere.
- The two young men died in the silo from asphyxiation. A permit confined space entry process that required the monitoring and ventilation of the space would most likely have helped prevented this tragic event.
- NIOSH sets minimum safe oxygen levels at 19.5 % (see paragraph and table below*).
- Carbon dioxide is a natural product of the haylage fermentation process and displaces oxygen in the silo. In a sealed oxygen-limiting silo, the atmosphere would mostly be carbon dioxide.
- Nitrogen oxides are another fermentation product that could be present and create a serious exposure for the entrants. (see FACE Fatal Facts discussion about Silo Filler’s Disease) (see paragraph below**)
- Carbon monoxide can be another hazard in the silo confined space. Carbon monoxide is most likely introduced into the silo head space via the tractor exhaust during the operation of the blower motor. Caution should be used during this process to minimize or eliminate this source of exposure.
(*The National Institute for Occupational Safety and Health (NIOSH) defines an oxygen-deficient atmosphere as any atmosphere containing oxygen at a concentration below 19.5% at sea level. NIOSH certification of air-line or air-purifying respirators is limited to those respirators used in atmospheres containing at least 19.5% oxygen, except for those air-line respirators equipped with auxiliary self-contained breathing apparatus (SCBA).
The minimum requirement of 19.5% oxygen at sea level provides an adequate amount of oxygen for most work assignments and includes a safety factor. The safety factor is needed because oxygen-deficient atmospheres offer little warning of the danger, and the continuous measurement of an oxygen-deficient atmosphere is difficult. At oxygen concentrations below 16% at sea level, decreased mental effectiveness, visual acuity, and muscular coordination occur.
At oxygen concentrations below 10%, loss of consciousness may occur, and below 6% oxygen, death will result. Often only mild subjective changes are noted by individuals exposed to low concentrations of oxygen, and collapse can occur without warning.)
Effects of Lack of Oxygen
Normal air is about 21% oxygen, 79% nitrogen and 0.03% carbon dioxide. The human body can sustain life at oxygen levels below 21%. Table 1 describes the human response to differing levels of oxygen in the atmosphere.
Oxygen Level (%) | Symptoms |
---|---|
12-16 | Breathing and pulse rate increased, muscular coordination slightly disturbed |
10-14 | Consciousness continues, emotional upsets, abnormal fatigue upon exertion, disturbed respiration |
6-10 | Nausea and vomiting, inability to move freely, loss of consciousness may occur, may collapse and although aware of circumstances be unable to move or cry out |
Below 6 | Convulsive movements, gasping respiration, respiration stops and a few minutes later heart action ceases |
(source: Patty’s Industrial Hygiene and Toxicology, Vol. 2C, 3rd edition) |
(** Nitrogen oxides (NOx) are produced as a result of the nitrate (NO3) content of the plant material. During the fermentation process, the plant nitrogen is released as nitric oxide (NO). Nitric oxide can mix with any oxygen in or around the silo forming nitrogen dioxide (NO2). When NO2 is inhaled, it dissolves with the moisture in your lungs and forms nitric acid, which "burns" your lungs. NO2 gas is reddish to yellowish brown and can have a bleach-like odor, however, visual and/or odor cues may not present themselves inside upright silos.)
Ventilation
In order to establish a “safe” atmosphere in a permit-required confined space it is recommended that “forced air” ventilation be used.
- The employer must ensure that a permit-required confined space has a ventilation system available for use for a confined space entry.
- The blower unit used and designed to deliver hay in the silo appeared to provide a reasonable level of forced air into the silo over time (see Appendix for ventilation testing results).
- Monitoring of the space is critical for safe entry, as discussed in the section above.
- Each confined space is different and ventilation effectiveness should be determined by testing the system and air flow.
- Persons should not enter a confined space until the testing and monitoring system says it is safe to do so.
- Continuous ventilation is recommended at all times during the entry.
- It is also important that the ventilation system effectively provides air to all areas of the confined space. Carbon dioxide and nitrogen oxides are heavier than air and can be present at high concentrations low on the surface of the stored feed and in pockets within the silo and thus continue to be a hazard for the entrants.
- Sometimes, depending on the source of the hazard and the effectiveness of the ventilation system, entrants might still need to wear “air-supplied" respirators for their personal safety while working in the confined space.
- The manufacturer, in their breather bag replacement process, instructs entrants to wear air-supplied respirators during the entry.
Communication
Another critical component of an effective and safe permit-required confined space entry is a good communication process.
- The communication process starts within the project planning stage and doesn’t end until the project is safely completed.
- Part of the communication process is to ask questions.
- Ask lots of questions, since this project has a recognized serious risk associated with a process that deals with an oxygen-limiting silo confined space entry.
- Questions need to be answered at the onset of the project, that describe the who, what, where, when, and how the project would be safely completed.
- If possible, contact several service or dealer representatives to learn about the process and the safest way to get the job done
- Do not rely on one source for a permit-entry confined space entry project.
- Contact the manufacturer to get the latest information and their recommendations on how to get the job done.
- It also would be a good idea to contact the Farm Bureau, farm extension service groups and DOSH/OSHA consultation to get information.
- Contact the local emergency team to discuss emergency processes.
- Contact other specialty service folks who can provide confined entry services to help with the project.
- Once the project plan has been decided upon and after some research on determining best practices, communicate the plan with the service representative/dealer and all workers that will participate in the project.
- Make sure all questions are answered and the project detail is clear for all parties.
Recommendation #2: Employers should review and use alternative methods so that confined space entry is not required.
Discussion: An important part of the focus for work being done within a permit-required confined space project should be how to safely perform routine and non-routine work and other activities that need to be done within the overall aspects of the operation, servicing and maintenance of the confined space.
The best plan is to have alternative processes and methods in place or available to accomplish maintenance or other work activities without requiring entry into the confined space. If the silo needs to be worked on or in, the employer should try to find a way of getting the work done without entering the silo. Get help from the silo manufacturer and other sources to develop a no-entry plan.
The manufacturer of the Harvestore® silo has an option for an external breather bag system. The external breather bag system is housed outside of the silo at ground level, making it logistically easier to maintain, service and replace the breather bags. The significant advantage here would be that one would not have to enter the silo to change out the breather bags.
The Harvestore® manufacturer also has an automatic fill system available. The fill system is designed to replace the need for climbing to the top of the silo and having to manually open and close the center fill and air exhaust hatches on the silo.
Entry into the silo could also be accomplished after the silo has been emptied of the feed (haylage). This would require a bit more planning by the farmer so that they would still be able to provide the required feed to the dairy cattle during the breather bag replacement process. Even though challenging, it would certainly be possible to plan the breather bag replacement using this method, given the fact that the farmer had two large capacity Harvestore® silos and other feed storage capability. Change-out of the breather bags after the silo had been emptied and properly ventilated would be done with the reduced atmospheric hazards created by the feed stock fermentation process.
The breather bag replacement process should follow the manufacturer’s recommended process using the safety cage device developed by the manufacturer.
Note: All required confined space procedures still need to be followed to include atmospheric testing and monitoring of the space to ensure it is safe for entry. Proper respiratory protection and fall prevention methods should be incorporated into the process when working on and in the silo.
Recommendation #3: Employers should consider contacting external expert consultants/contractors to help with confined space management and confined space entry process.
Discussion: A good way to develop a permit-required confined space entry plan, and maybe the best way, is to use external consultants who have the expertise and the qualifications to put together this critical element of providing a safe entry process for work that needs to be done in a confined space.
Outside consultants from organizations such as the DOSH/OSHA Consultation group, the Farm Bureau, and many independent consulting groups can help put together a comprehensive confined space risk evaluation and permit-required entry plan for not just silos but for all the various confined spaces on the farm.
A permit-required confined space needs to be tested and monitored by a qualified person prior to entry to determine if it is safe to enter the confined space. External consultants can provide the expertise and the proper equipment to help facilitate the confined space monitoring process.
Outside consultants can provide not only advice on the identification of confined spaces but can also help with training. Consultants may also help with the control mechanisms needed to deal with identified hazards, putting together a permit system for permit-required confined spaces, and with an emergency plan that needs to be established with each permit-required confined space.
Respirators might be needed for specific permit-required confined space entries. Outside consultants can help with this element of the confined space process as well.
Recommendation #4: Employers and contractors need to follow manufacturers’ recommended maintenance procedures.
Discussion: We strongly recommend that employers and contractors be very familiar with the manufacturer’s recommended service and maintenance guidance procedures. The employer or contractor needs to have the latest versions of manufacturer’s guidelines that contain the newest information that the manufacturer has available.
They should contact the manufacturer prior to any critical maintenance service or repair dealing with the manufacturer’s equipment to discuss key elements of the process. This is one part of a maintenance process that is often missed or ignored by employers, workers, contractors and maintenance people.
The manufacturer has a cage that is inserted into the silo hatch that they recommend to be used when replacing internal breather bags. If the cage apparatus had been used then the two 16-year-olds might have had to wait and help the service representative in the installation of the cage before they did any prep work without the service representative.
Manufacturers need to train all authorized dealers and their service personnel on how to safely and effectively repair, maintain and service their products. This is especially important when dealing with high hazard operations such as confined space entry.
The manufacturer should keep a record of this training and provide follow up information or additional training regarding new processes as needed. Even though the dealer or service representative may not be a part of the manufacturer’s operation, as was the case in this incident, they do reflect and represent the integrity of the manufacturer through their interaction with customers when they are working with the manufacturer’s product. Often the employer or owner is either untrained or has minimal knowledge and also often has very little experience on non-routine maintenance and service and will count on the service representative to provide expert advice.
Recommendation #5: Employers need to have processes in place that prevent unauthorized entry.
Discussion: When dealing with any permit-required confined space, the employer needs to have processes and mechanisms in place that prevent unauthorized entry into a confined space. One of the basic control mechanisms is the “permit” requirement portion of the permit-required confined space entry process.
When a space has been determined to be a permit-required confined space, no-one is allowed to enter the space until the safe entry requirements on the permit are met. A confined space permit can also function as a confined space safety check list that must be completed by authorized entry personnel.
It is also recommended that physical barriers be put in to help prevent unauthorized persons from entering or inadvertently falling into a confined space. The barriers need to be controlled by the employer using mechanisms such as a “lock out program” along with locking devices to help secure the barriers. The locking devices located near entry points to the silos and other confined spaces can prevent unauthorized access to those spaces.
The manufacturer of the Harvestore® silo indicated that they have available and install a safety device on their relatively more recent vintage silos to help prevent entry through open hatches. The device is a red bar that is installed directly across the silo hatch opening. The bar is designed to prevent direct and inadvertent entry into the space and can be used as a reminder to follow proper entry procedures prior to entry.
Although it was not determined by the investigation, it is not beyond the realm of possibility that the first young man might have fallen through the hatch into the silo as he was checking the level of hay in the silo. The second victim quite likely entered to help the first victim. The farm owner conducting his own investigation demonstrated that it was possible that a person the size of the two victims could fall through the silo hatches.
Another scenario that might have taken place was that one of the boys jumped into the silo to prepare it for the breather replacement, thinking that the hay was still near 3 feet from the top as they had left it the past Saturday.
The problem on that incident morning was the farm had continued to draw haylage from the bottom of this silo (silo #1) as silo #2’s unloader was still not working. The hay was 12 feet from the top of the silo and not three feet as the first victim might have remembered. The other young man again probably went in to help his friend in this scenario. There was no ladder for either of the young men to use to get out of the silo.
The manufacturer had warning signs on each of the hatch openings indicating the oxygen-deficient danger in the silo. A lock out system could have been used so that only authorized persons could have entered the permit-required confined space (i.e., silo) and only under an employer controlled access (i.e., permit) process that ensured the entry was safe and all hazardous elements of the confined space were addressed prior to entry.
Recommendation #6: Employers need to maintain close supervision of all teen employees and contractors
Discussion: Young workers often are at increased risk for injury in the work place according to NIOSH.
NIOSH indicates that factors for this increased risk include:
- Young workers commonly perform tasks without question for which they have not received proper training in order to display responsibility, maturity, or independence in the eyes of the employer.
- Young workers often lack the experience and physical maturity needed for certain tasks.
- Young workers’ continuing rapid growth of organ and musculoskeletal systems can make them more likely to be harmed by hazardous substances or develop cumulative trauma.
Employers must take an active role in the supervision of young workers. They must recognize the hazards that young workers are exposed to, provide all necessary training needed to do their jobs, provide constant reminders of what jobs or tasks they can do and not do, and provide the necessary oversight and supervision needed so that the young workers can, within limits and proper controls, perform only the jobs and tasks that they are asked and expected to do.
Permit–required confined space entries can be very unforgiving places to work. Persons 18 and under should never be part of a permit-required confined space entry process on the farm or any other occupational setting. Make sure that you check Washington State Labor and Industries employment requirements for teen workers.
Do not assume that any contractor or representative is current on manufacturer recommendations or knows appropriate safety procedures for your workplace. Make sure that anyone working on your site has been trained and follows safe procedures for any hazardous work such as in confined spaces.
Recommendation #7: All permit-required confined spaces must have detailed rescue processes and personnel in place.
Discussion: Rescue procedures need to be established for every permit-required confined space. Confined space rescues are technically challenging for any situation and especially challenging from a 90-foot tall silo. Both of these situations combined together can be very risky for the rescuer.
It is critical for the safety of confined space entrants and potential rescuers that a well defined rescue plan and process be in place before any permit-required confined space entry takes place. History shows that a high percentage of would-be rescuers die from uncontrolled rescue attempts. Rescuers need to be properly trained and equipped for rescue so that they do not become victims of the confined space.
Any permit-required confined space can necessitate a hazardous rescue process, but with proper training, and with a clear recognition of the hazards, the rescue process can be safely performed with reduced risk for the rescuers. The goal of any rescue attempt is to successfully extract a victim and the rescuer out of a harmful situation as quickly as possible.
If a permit process was in place which would have helped reduce the risk for the entrants, and if the plan included a confined space attendant and rescue plan, then the fatalities in this incident might have been prevented. The best rescue process is to have a plan in place where the rescuer does not have to enter the confined space to perform the rescue. If a confined space entry can be set up with the entrant wearing a harness and retrieval line attached to a mechanical retrieval device, the rescue process can greatly reduce the hazard to the rescuer and often can help facilitate a much quicker rescue of the entrant/victim.
Proper training and planning will make any permit-required confined space entry much, much safer. Planning and training are critical parts of a safe and successful confined space entry. This is especially true for rural communities with volunteer emergency rescue response teams, like the one described in this incident. Not having the proper training can possibly cost the lives of the confined space entrants and the rescuers.
Local businesses should set up communication and planning sessions with area emergency rescue services to plan and even practice confined rescue if possible. Information about the types and hazards associated with each farm and farm activities located in the community rescue radius can help expedite a rescue process.
Valuable information that the rescue teams need to have in advance of a silo emergency, for example, would be to know the name of the manufacturer, the type and brand of the silo and the unloader. They should know what is normally stored in the silo; the dimensions and age of the silo; and any special characteristics of the silo such as is it an oxygen-limiting silo, or a conventional silo and what other hazards should they be aware of when dealing with the farm’s silo in an emergency response. The silo manufacturer should also be considered as a resource and be consulted in developing an emergency plan.
Local emergency teams need to know the logistics of the farm operations and other important information related to any confined spaces that they might have a need to respond to and provide emergency services. They need to be trained, prepared and equipped to deal with a variety of farm rescue situations and/or know of other resources that might be available in the area to provide additional and, perhaps, specialized assistance.
Back to Top
Acknowledgements
Though we are not able to acknowledge specific individuals for their invaluable input into this document, we would like to recognize the following for their help and support to the FACE process:
- The Farm Family
- DOSH Enforcement
- DOSH Policy & Technical Services staff
- Federal Face Program Management (NIOSH)
- Safety & Health Assessment & Research for Prevention (SHARP)
- Washington State Farm Bureau
- Silo Manufacturer
- Washington State Attorney Generals Office
Photographs
![]() |
Photo 1. A view of the top of the silo with ladder cage and chute extended after filling. |
![]() |
Photo 2. The silo access hatch on the top of the silo. |
![]() |
Photo 3. A view of the silo from ground-level. |
Appendix A and B
Appendix A - Air Sampling Results from the Silo Under Similar Conditions to the Incident PDF (13 pages)
Appendix B - DOSH Guidance on Controlling Confined Space Hazards PDF (25 pages)

Washington FACE Program/SHARP
To contact Washington State FACE program personnel regarding State-based FACE reports, please use information listed on the Contact Sheet on the NIOSH FACE web site Please contact In-house FACE program personnel regarding In-house FACE reports and to gain assistance when State-FACE program personnel cannot be reached.
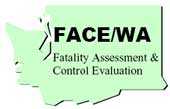
- Page last reviewed: November 18, 2015
- Page last updated: October 15, 2014
- Content source:
- National Institute for Occupational Safety and Health Division of Safety Research