Mining Publication: Technology News 559 - Mobile Dry Scrubber Provides Cleaner Air for Downwind Roof Bolter
Summary
A self-tramming, remotely controlled mobile dry scrubber (DS) was developed by J.H. Fletcher and Co. (Fletcher) under a NIOSH contract to reduce exposure of miners to airborne dust. Roof bolter operator overexposure to respirable dust can occur when bolting downwind of the continuous miner (CM) during its operation. Laboratory and underground testing shows that the DS can provide cleaner air at these downwind roof bolter locations.
By Scott Klima
Background
Coal mine worker overexposure to coal and quartz dust continues to be a problem at underground coal mines. Effective in 2016, the U.S. Mine Safety and Health Administration (MSHA) changed the regulatory standard for coal mine worker respirable dust exposure from 2.0 mg/m3 average during an eight-hour shift to 1.5 mg/m3 average over the actual working shift. MSHA inspector dust samples from 2009 to 2012 showed that 3.7% of roof bolter operators exceeded the new 1.5 mg/m3 dust standard, and 10.6% of roof bolter operators exceeded the quartz standard.
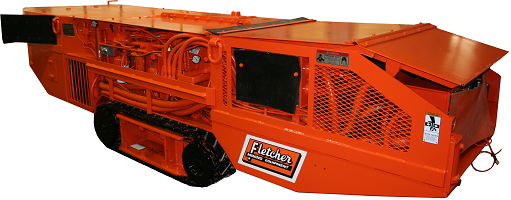
Figure 1. Photo of the dry scrubber, commercially available from Fletcher (photo by J.H. Fletcher & Co.).
On-board flooded bed scrubbers on CMs are proven, efficient collectors of respirable dust. However, dust bypassing the scrubber, as well as exhaust air from CMs not equipped with scrubbers, may expose roof bolter operators who work downwind of the CM to high levels of respirable dust. These dust concentrations can greatly exceed regulatory standards and overexpose roof bolter operators. To combat this, the National Institute for Occupational Safety and Health (NIOSH) contracted with Fletcher to develop a self-tramming, stand-alone dry scrubber (see Figure 1), which can reduce roof bolter operator dust exposure by cleaning dust-laden air before it enters the bolter workplace entry.
Laboratory and Field Testing
Laboratory testing was conducted at NIOSH to examine the DS’s operational performance. This included airflow measurement, dust removal efficiency, filter loading, and sound pressure level testing. All laboratory testing was conducted with a straight exhaust duct. A 90-degree angled discharge duct is also available to redirect the exhaust air to either side of the scrubber. Field testing was conducted in an underground mine to examine its effectiveness in reducing dust levels at the face area downwind of the CM.
To determine the average air velocity and airflow quantity of the DS, a 32-point equal area air velocity sampling grid across the discharge duct was used. A hot wire anemometer and pitot tube were used to measure the air velocities across the sampling grid to determine the air quantity of the DS at planned dust testing quantities of 3,000 and 9,000 ft3/min.
Dust removal efficiency testing was conducted on the DS in NIOSH’s CM gallery. Coal dust was introduced at the entrance of the gallery intake and was drawn down the entry by the scrubber at airflows of 3,000 and 9,000 ft3/min. Respirable dust concentrations were measured downwind and upwind of the DS with coal mine dust personal sampling units (CMDPSU). These were made up of an air sampling pump pulling dust-laden air through a cyclone and depositing the respirable fraction onto a pre-weighed filter. Each sampling location contained two CMDPSUs and one real-time Personal Data Ram (PDR) instrument. The dust concentrations measured downwind and upwind of the DS were used to determine its respirable dust removal efficiency.
The disposable scrubber filter cartridges installed in the DS were successively tested during four one-hour tests at scrubber airflows of 3,000 and 9,000 ft3/min. The filters were further evaluated twice during subsequent two-hour tests at the scrubber airflow of 9,000 ft3/min to observe scrubber performance during additional filter dust loading. A sound pressure level meter was used to measure the sound pressure level of the DS while operating at multiple scrubber airflow settings with unloaded and loaded filters.
Underground field testing was performed at two active mechanized mining units (MMUs) that used blowing face ventilation with flooded-bed scrubbers on the CM. The DS was placed in the last open crosscut of the section return to examine its effectiveness at lowering respirable dust concentrations downwind of mining activities (Figure 2). The roof bolter was monitored using area sampling to examine respirable dust concentrations when working upwind and downwind of the CM during production, and other dust sampling locations were used for evaluating the respirable dust reductions when operating the DS. PDR dust concentrations were gravimetrically calibrated to determine dust concentrations during the particular mining activities. Time studies and section locations of the CM and roof bolter machines were used to coordinate and determine the gravimetrically adjusted PDR dust concentrations during scrubber operation and roof bolter activities with respect to the CM operation.
Test Results
NIOSH laboratory testing of the DS showed that it averaged greater than 95% dust removal efficiency with disposable filters. The scrubber fan maintained a relatively consistent airflow near the targeted 3,000 and 9,000 ft3/min airflow rates until reaching 10.5 in. water gauge of filter differential pressure at 8,420 ft3/min of scrubber airflow quantity. At this point the scrubber airflow decreased with additional dust loading because the fan had reached its maximum horsepower rating. Laboratory sound pressure level measurements for the scrubber showed that loaded filters increased sound pressure levels as compared to clean filters. With loaded filters at 6,000 ft3/min of scrubber airflow, the DS reached a 90 dB(A) sound pressure level measured 10 ft from the scrubber outlet.
Field testing of the DS with disposable filters was completed at two underground MMUs. Time-weighted average respirable dust concentrations were measured at each MMU with respect to CM activities. The average roof bolter machine dust concentrations at MMU 1 and 2 were 0.59 and 0.17 mg/m3, respectively, when operating upwind of the CM as compared to 1.80 and 1.60 mg/m3, respectively, when operating downwind of the CM and upwind of the DS. Overall, the DS was able to clean a portion of the section return air, reducing the dust concentrations at the face areas downwind of the CM for all cuts by 49.1% at MMU 1 and 50.5% at MMU 2.
In order to ascertain the DS’s respirable dust removal efficiency underground, the face area CMDPSU and PDR instruments were placed directly into the DS exhaust discharge air for 2 to 5 minutes at the end of several shifts. The measured DS exhaust concentrations at MMU 1 and 2 averaged 0.13 and 0.01 mg/m3, respectively, while their corresponding upwind dust concentrations averaged 1.87 and 1.08 mg/m3, thereby yielding DS dust collection efficiencies of 93.2% and 99.2%, respectively. This shows that the clean DS exhaust airflow was mixed with some of the dirty return airflow being delivered to the face. This airflow mixing was further exhibited by the DS’s 1.4 to 1.7 face airflow quantity improvement over the initial airflow quantities without the DS operating.
Based on the above results, the DS appears to be a new viable dust control method to combat roof bolter operator dust exposures when operating downwind of the continuous miner.
Mobile Dry Scrubber Availability
The DS is engineered to operate between the mine rib and ventilation curtain, downwind of the CM and upwind of the roof bolter. It is commercially available from Fletcher and is MSHA permissible. A tubing discharge configuration is also available for the dry scrubber.
For More Information
For more information on the dry scrubber, contact the NIOSH Mining Program (mining@cdc.gov).
See Also
- Best Practices for Controlling Respirable Dust in Coal Mines
- Development of a canopy air curtain to reduce roof bolters’ dust exposure
- Development of a Roof Bolter Canopy Air Curtain for Respirable Dust Control
- Development of Dust Control Units for Underground Coal Mines
- Impact on Respirable Dust Levels When Operating a Flooded-bed Scrubber in 20-foot Cuts
- Laboratory and Field Evaluation of Dust Collector Bags for Reducing Dust Exposure of Roof Bolter Operators
- Laboratory Evaluation of a Canopy Air Curtain for Controlling Occupational Exposures of Roof Bolters
- Respirable Quartz Hazard Associated with Coal Mine Roof Bolter Dust
- Roof Screening: Best Practices and Roof Bolting Machines
- Technology News 509 - A New Method to Clean Dust From Soiled Work Clothes
- Page last reviewed: 10/12/2017
- Page last updated: 10/12/2017
- Content source: National Institute for Occupational Safety and Health, Mining Program