SILICA
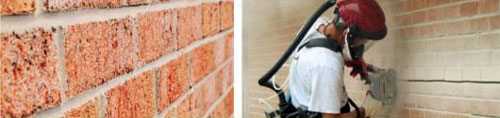
Engineering Controls for Silica in Construction
Tuckpointing
NIOSH has identified control measures to reduce worker exposure to hazardous dust containing respirable crystalline silica (RCS) during tuckpointing. The Tuckpointing without Controls video shows a worker exposed to high concentrations of hazardous dust while using a tuckpointing grinder without dust controls. The units are milligrams of respirable dust per cubic meter of air (mg/m3).
Download the Tuckpointing without Controlsvideo
Studies [1] [2] have shown that using a local exhaust ventilation dust control can reduce respirable crystalline silica dust exposure by 5-20 times.The local exhaust ventilation dust control includes a shroud that encloses most of the grinding wheel, a length of flexible hose, and an industrial vacuum cleaner.The recommended features of a local exhaust control are provided below.
Vacuum Cleaners
The type of vacuum cleaner may vary.It should have a minimum air-flow rate of 65 cubic feet per minute (cfm), but the objective is to provide an air flow of 80 cfm to achieve effective dust control.Use a vacuum cleaner with a cyclonic preseparator (cyclone) to keep debris from reaching the final filters. This will enable the vacuum cleaner to maintain an adequate airflow, which will facilitate dust capture and transport [3].
A pressure gauge can be used to monitor the performance of the vacuum cleaner. If the vacuum cleaner does not have a pressure gauge, workers can monitor the air flow by checking to see if a dust plume is escaping from around the shroud. If dust is escaping, turn off the unit and clean or change the filter as recommended by the manufacturer. The final filter should be a high-efficiency particulate air (HEPA) filter to reduce the chance of releasing dust containing crystalline silica from the vacuum into the worksite.
Hose
A 2-inch diameter hose with a smooth interior and a length of no more than 15 feet provides adequate air flow to capture and transport the mortar dust. The hose should have as few elbows or turns as possible.
Shroud and Grinder
The shroud should totally enclose the spaces around the exhaust entry point for the hose. The shroud should have an entry point for the hose that matches the diameter of the hose. Some tuckpointing grinders come with an attached shroud, otherwise it must be purchased separately.
The Tuckpointing with Local Exhaust Ventilation Controls video clip demonstrates the effectiveness of this type of control. Note the reduced levels of respirable dust in the right hand bar.
Download the Tuckpointing with Local Exhaust Ventilation Controls video
Work Practices
- Keep the exhaust entry point flat against the surface.
- Shake the hose as needed to loosen the settled dust and prevent the hose from clogging.
- Work against the rotation of the blade. The tool must be flat and positioned so that the dust from grinding is blown into the exhaust hose.
- Change vacuum cleaner bags before they leak, break, or cause too much resistance to air flow.
- Put the vacuum cleaner below the work level to keep dust from falling out of the hose.
- Even when the amount of hazardous dust has been decreased by the control, less restrictive respirators may still be necessary to reduce exposure to crystalline silica below the NIOSH REL of 50µg/m3. Exposure monitoring is necessary to determine what type of respirator is needed.
Additional Information
For more information about dust controls for tuckpointing see:
- Field evaluation of an engineering control for respirable crystalline silicaexposures during mortar removal.
Journal of Occupational Environmental Hygiene: 2007 / 4:875–887. - Protecting tuckpointing workers from silica dust: draft recommendations for a ventilated grinder.
Silver Spring, MD: The Center to Protect Workers’ Rights (2005). -
A numerical and experimental investigation of crystalline silica exposure control during tuck pointing
Journal of Occupational Environmental Hygiene: 2006 / 3:366–378. -
Control of Hazardous Dust During Tuckpointing
DHHS (NIOSH) Publication Number 2008-126 -
Control del polvo peligroso que se genera durante los procesos de reparación de mortero
DHHS (NIOSH) publicación N.º 2008-126
- Page last reviewed: July 29, 2013
- Page last updated: November 9, 2016
- Content source:
- National Institute for Occupational Safety and Health Division of Applied Research and Technology